Convertisseur (métallurgie)
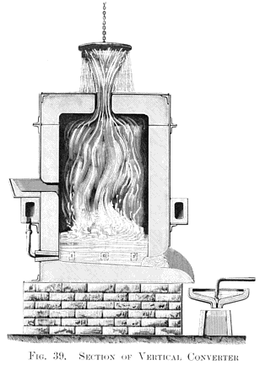
Un convertisseur est un four servant de réacteur chimique pour une opération d'affinage des métaux en fusion.
Apparition du convertisseur[modifier | modifier le code]
Le convertisseur apparaît avec l'invention du procédé Bessemer. Jusqu'ici l'affinage de la fonte en acier se faisait à l'état solide (fabrication d'acier naturel, puddlage, etc.), mais le four-réacteur inventé par Henry Bessemer est si différent des procédés connus jusqu'alors qu'un nouveau terme apparaît pour le désigner. Par extension, tous les appareils d'affinage des métaux en fusion qui en dérivent prennent le même nom. Les fours d'affinage du procédé Martin-Siemens sont d'un principe très différent, mais comme leur fonction est la même, ils ont pris — dans la langue française — le même nom.
On distingue deux types de convertisseurs :
- les cornues à soufflage d'air sous un bain de fonte liquide. Le procédé fut inventé par Henry Bessemer en 1855. Sidney Gilchrist Thomas le modernise en 1877 avec un revêtement réfractaire basique, le rendant ainsi capable d'affiner les fontes issues de minerais phosphoreux ;
- les fours à réverbère inventés par Carl Wilhelm Siemens en 1857. Pierre-Émile Martin les améliore en 1865.
-
Principe de fonctionnement du procédé Bessemer/Thomas.
-
Convertisseur Bessemer au Kelham Island Museum de Sheffield.
-
Convertisseur Thomas exposé à Dortmund.
-
Four Martin-Siemens du Musée de l'industrie de Brandebourg.

Évolutions[modifier | modifier le code]
Sidérurgie[modifier | modifier le code]
Ces deux technologies ont coexisté jusqu'à l'avènement des convertisseurs fonctionnant à l'oxygène pur, qui sont une amélioration des cornues Bessemer-Thomas. Quant au four Martin-Siemens, dont la polyvalence lui permet d'affiner la fonte comme de recycler les ferrailles, il a été remplacé par le four à arc électrique, exclusivement destiné au recyclage de ferrailles. On recense actuellement :
- les convertisseurs à soufflage par le bas, au moyen de tuyères métalliques refroidies grâce au craquage d'hydrocarbures. Ce procédé, efficace mais très difficile à maîtriser, est en cours de disparition ;
- les convertisseurs à soufflage latéral, comme les fours Kaldo, où le brassage de l'acier liquide est assuré par la rotation de la cornue, imitant la cinématique d'une bétonnière. Cette solution a disparu pour des raisons économiques, le coût de renouvellement des réfractaires, soumis à des chocs thermiques répétés, étant prohibitif ;
- les convertisseurs à soufflage par le haut, au moyen d'une lance. Ces convertisseurs s'inspirent tous du type LD (Linz-Donawitz), développé en 1952 par Voestalpine. Le brassage du métal liquide est assuré par la réaction chimique elle-même ;
- le type AOD (Argon Oxygen Decarburization) qui est une variante du LD, destiné à l'élaboration des aciers inoxydables. Dans ce convertisseur, l'oxygène est dilué dans de l'argon en proportion variable.
-
Convertisseur à soufflage par le bas de type LWS à La Providence Réhon
-
Principe de fonctionnement du convertisseur LD.
Quantités de matières premières (en kg) consommées par tonne d'acier produite | Énergie et apport en O2 | ||||||||
---|---|---|---|---|---|---|---|---|---|
Procédé | Fonte brute | Ferraille | Additions diverses (laitier et métal) |
Mise au mille | Combustible (MJ/t) | Oxygène (m³/t) | |||
Liquide | Solide | Acier | Fonte moulée | ||||||
Procédé Martin-Siemens | Acide | 182 | 848 | 47 | 85 | 1 162 | 6 200 | ||
Basique | 493 | 93 | 492 | 32 | 185 | 1 299 | 4 280 | ||
Convertisseurs à l'oxygène | Kaldo | 583 | 11 | 425 | 137 | 127 | 1 283 | 65 | |
LD | 838 | 12 | 282 | 4 | 316 | 1 252 | 57 | ||
Rotor | 840 | 160 (minerai de fer) | NC* | NC | 72,5 | ||||
Four à arc électrique | 19 | 32 | 1 002 | 23 | 105 | 1 181 | 1 283 (485 kWh) | 4 |
NC: Non Communiqué
Métallurgie extractive des métaux non ferreux[modifier | modifier le code]
Le convertisseur Manhès-David, est développé dans les années 1870 par l'industriel français Pierre Manhès et son ingénieur Paul David, pour affiner les mattes de cuivre. Inspiré du procédé Bessemer, il consiste en l'utilisation d'un convertisseur Bessemer pour oxyder avec de l'air les éléments chimiques indésirables (essentiellement le fer et le soufre) contenus dans la matte afin de l'affiner pour obtenir du cuivre pur. L'adaptation la plus notable consiste en des tuyères latérales, puis en une forme de cylindre horizontal. En 1905, les américains William H. Peirce et Elias Anton Cappelen Smith augmentent significativement ses performances en changeant son revêtement réfractaire[3]. Au début du XXIe siècle les convertisseurs Peirce-Smith interviennent dans 90 % de l'extraction du cuivre[4], et dans 60 % de l'extraction du nickel[5].
-
Convertisseur Manhès-David vertical en 1895 à Grand Sudbury. Sa filiation avec la cornue du convertisseur Bessemer est évidente.
-
Principe du convertisseur Manhès-David horizontal, en 1912.
-
Convertisseur Peirce-Smith en 1954 à Mount Isa.
Notes et références[modifier | modifier le code]
- (en) Hilary Bauerman, F.G.S (ill. J. B. Jordan), A treatise of the Metallurgy of Iron, Londres, Crosby Lockwood and Son, coll. « Weale's scientific & technical series / Mining and metallurgy », , 6e éd. (1re éd. 1868) (lire en ligne), p. 436
- (en) Colin J. Smithells, Metals Reference Book, 5, , 1582 p. (ISBN 0-408-70627-9, lire en ligne), p. 1432 ; 1434
- (en) Donald M. Levy, Modern Copper Smelting, C. Griffin & company, limited, (lire en ligne), p. 192-194
- (en) Marc E. Schlesinger, Matthew J. King, Kathryn C. Sole et William G. I. Davenport, Extractive Metallurgy of Copper, Elsevier, , 5e éd., 455 p. (ISBN 978-0-08-096789-9, lire en ligne), p. 143
- (en) Frank K. Krundwell, Michael S. Moats, Venkoba Ramachandran, Timothy G. Robinson et William G. Davenport, Extractive Metallurgy of Nickel, Cobalt and Platinum Group Metals, Elsevier, , 610 p. (ISBN 978-0-08-096809-4, lire en ligne), p. 2 ; 15
Voir également[modifier | modifier le code]
Articles connexes[modifier | modifier le code]
Généralités :
En sidérurgie :
- Histoire de la production de l'acier
- Fabrication de l'acier
- Procédé Bessemer, Procédé Thomas, Procédé Kaldo, Procédé LD
- Procédé Martin-Siemens
- Aciérie
- Gaz de convertisseur
Dans la métallurgie extractive des métaux non ferreux :